
News & Event
01Column
The misunderstanding that it is too difficult to infuse the matrix to 3D woven preform.
I have written in previous column as one of misunderstanding of "Urban Legend" that 3D woven preform has isostatic structure.
However, it has more "Urban legend" for 3D woven preform.
When I was studying composites materials at many years ago, as the most famous misconception about 3D woven preform was it has closed pores inside.
I think that this urban legend was born from an extended abstract at "14th Biennial Conference on Carbone".
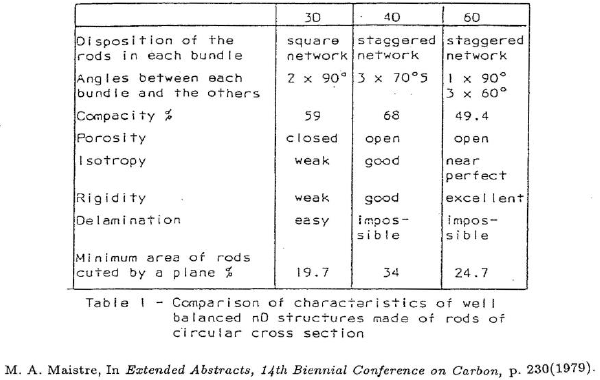
This study has been analyzing in detail structure about various multi-directional composites.
Although 3-directional orthogonal structure forms closed pore at the intersection, the open pore is formed at four or more directional structure, are shown in Table 1.
From this study, 3D orthogonal structure that has closed pore inside is difficult to infuse the matrix, therefore it had misunderstood that 3D woven preform was also too difficult to infuse the resin.
However, since the table caption has been written in "Structure made of rods circular cross section", it has not mentioned about 3D woven preform.
From this background, we have investigated about pore structure and distribution about 3D preform.
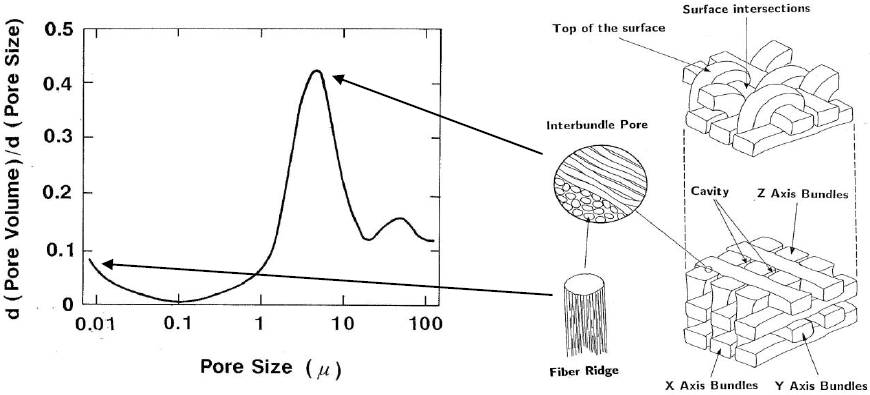
Figure is shown the measurement result of pore distribution structure at 3D woven preform by using the Mercury porosimetry method.
Since the total mercury infusion value was the same of 3D Preform pore value that was calculated by fiber volume fraction, this was one of result that the liquid materials could be infused inside of this 3D woven preform structure.
It has three peaks on this figure, so it was observed that 3D preform has three kind of pore structure.
We have considered these results as follows.
The large pore distribution of 70 micron shows the surface rough area of preform.
The largest peaks at 7 micron will be shown the gap between each filament.
It could be measured only entrance pore size by this mercury porosimetry method, so this peak value also is included the inside space which was called "Cavity" as closed pore.
This result is shown the matrix can be infused through this gap easily, because the structure of this gap which is which is the space between fiber is the same of normal UD or 2D materials.
The smallest pore distribution is shown in the fiber surface ridge, so because of this pore size is too small compared with fiber size of 7 micron.
From these results, it shows that 3D woven preform is not have any trouble to infuse the matrix, so one urban legend has disappeared.
At the next time, the misunderstanding at measurement method of mechanical property at 3D composite would like to be discussed.
Thanks and Best regards,
Editor
02Exhibitions
-
- March 4-6, 2025
-
JEC World at "Nord Villepinte" Paris, France Shikibo Booth Hall6 B43
-
- March 5-7, 2024
-
JEC World at "Nord Villepinte" Paris, France Shikibo Booth Hall6 B43
-
- March 8-10, 2022
-
JEC World at "Nord Villepinte" Paris, France
-
- June 1-2, 2021
-
JEC COMPOSITES CONNECT Virtual exhibition
03Conference Activities & Talks
-
- 2017
-
21st International Cinference on Composite Materials (ICCM-21) (in Xi'an, China) Interlaminar reinforcement of CFRP laminates using Zanchor process
Ryoya Sugihara, Kohei Konda, Naoki Mori, Takayuki Kusaka (Ritsumeikan University)
Taishi Isono, Masaki Hojo (Kyoto University)
Toshifumi Fujii, Kazuo Nakajima, Yasuhiko Iwasaki (Shikibo Ltd.)
-
- 2013
-
Japanese-European Symposium on Composite Materials 11/4 - 11/6 Development of low cost preform for aircraft application,
T. Tanamura,N.Sakaki